People often ask us if our goal is to replace the existing EV battery cell testing and inspection technologies. It’s a fair question, given the powerful predictive analytics and rich insights our EchoStat® battery test solution delivers at factory-ready rates. The answer is no—there is still a critical need for conventional testing technologies.
Essential tools like vision, electrical, X-rays and CTs are dramatically enhanced by adding EchoStat to your battery test system. When applied during cell production, EchoStat improves on the intelligence that existing technologies provide in three important ways. With these insights, manufacturers can improve the reliability, safety, and performance of lithium-ion EV batteries at the scale we need for the world’s shift toward a cleaner energy future. Read on to learn more about each of the three key enhancements.
1. Richer Battery Cell Testing Data
Cell performance testing and CT inspection can only be done on a small percentage of cells produced due to their speed and cost. Investing in these tests for a larger percentage means significant additional cost to the manufacturer, in the tens of millions of dollars per 1 GWh of production capacity. That leaves major gaps in knowledge about production quality. EchoStat, because of its speed and non-destructive nature, can provide 100% inspection of cells produced with rich insights at a lower cost, addressing the knowledge gap and increasing confidence in cell quality.
Using ultrasound technology and machine learning, EchoStat delivers spatially resolved data in under six seconds, including more than 60 metrics related to physical features in a cell. We combine these into descriptive scores that provide more comprehensive insights than standard X-ray, visual, or electrical testing. And because these scans penetrate through the entire cell, they can identify sub-surface or internal issues, whereas standard vision methods are limited to surface-level defects.
2. Precise Predictive Analytics
Our advanced EchoStat solution uses acoustic scans to create a snapshot of battery cells before the Quality Assurance/Quality Control stage. That means that defects that arise during the manufacturing process are discovered during the manufacturing process, rather than waiting days or even weeks for end-of-line electrical testing.
What’s more, while standard electrical methods at the end of the manufacturing line can quickly and cost-effectively test voltage and resistance tests, they do not correlate well to cell performance. We take the spatially resolved data generated during that multi-second acoustic snapshot and feed it into an array of unparalleled predictive analytics models. These models aggregate data from cell finishing to QA/QC—providing unmatched insights to improve process quality monitoring and control.
The results speak for themselves. During various in-factory trials, EchoStat’s performance prediction models have proven accuracy ranging from 83 to 98 percent. In those same trials, our anomaly detection models have identified cells containing separator defects with greater than 90 percent accuracy, and we continue to work with manufacturers to include additional defect types into our detection capabilities.
3. Faster Battery Cell Testing and Improved Quality Control
Speed is a crucial aspect of manufacturing high-quality, reliable and affordable EV batteries at scale. EchoStat’s combination of powerful data and a much shorter feedback loop enables battery cell manufacturers to detect problems with their processes more effectively and optimize them more efficiently. Streamlining and optimizing QC like this results in increased line efficiency, lower production costs, and, eventually, more batteries available to power the EV revolution.
Cell performance is dependent on success during multiple stages of manufacturing, including electrode fabrication, cell assembly, electrolyte fill and soak, and formation. While there are standard testing methods that can provide detail on all those aspects, they’re typically quite slow. CT scans, for example, deliver quality, high-resolution 3D images, but can take two to four hours to examine each cell. Compare that to EchoStat which, when integrated into the production line, delivers rich insights in real time.
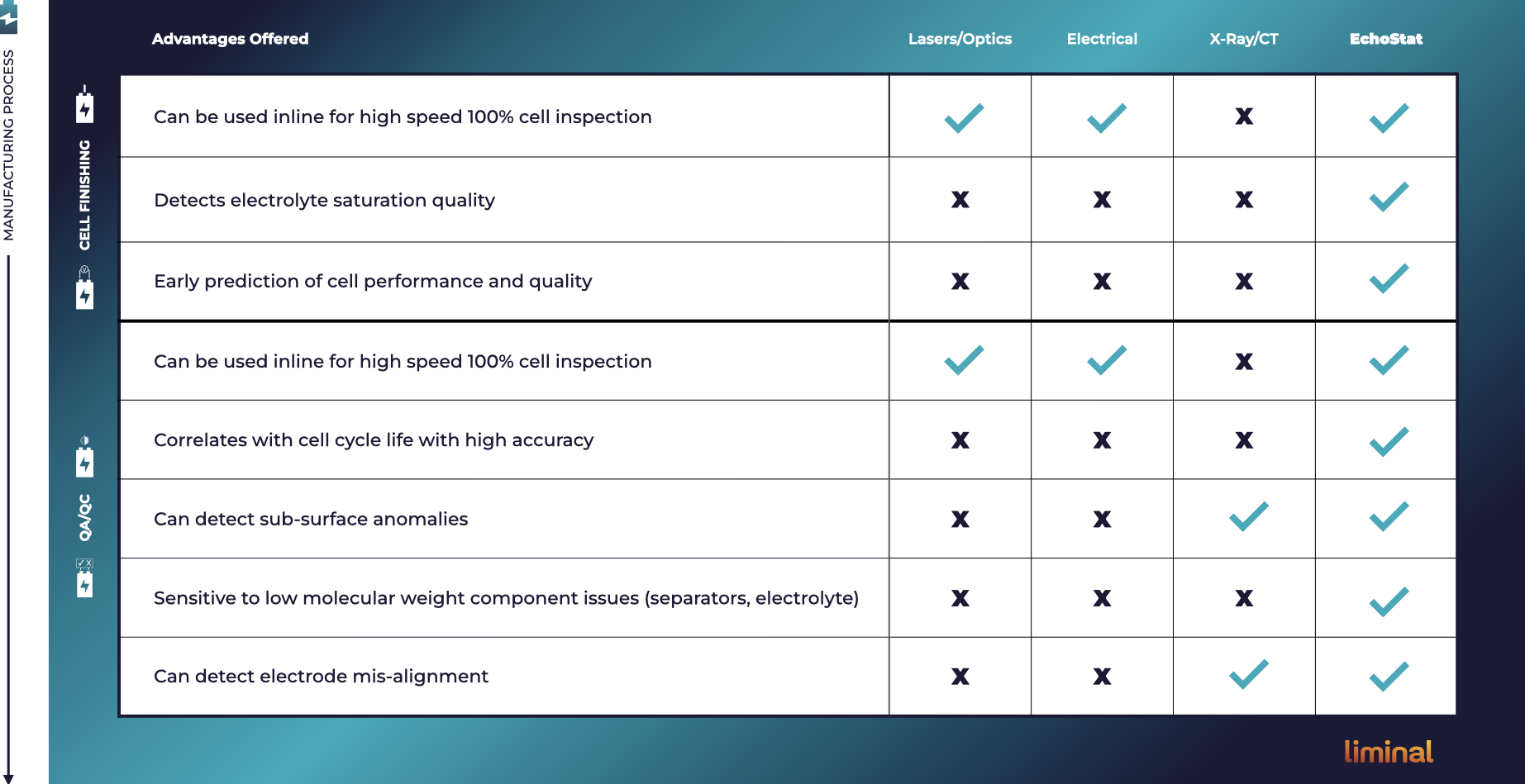
Delivering Safe, Reliable Batteries for a Clean Energy Future
The unprecedented demand from the electric vehicle and energy storage industries is a paradigm shift for the battery manufacturing industry. Manufacturers need to reduce costs and improve the quality of EV battery cells to meet rising demand, and advanced inspection throughout the entire manufacturing process is key to making that happen.
Improved testing and inspection methods like EchoStat can identify errant cells with greater precision than ever before, ensuring no bad cell escapes the plant and makes its way into an EV. EchoStat’s unique technological advantages unlock value every step of the way, enabling battery manufacturers to quickly scale production of high-quality, reliable batteries and avoid costly recalls.